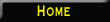
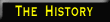
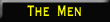
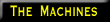
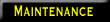
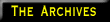
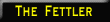
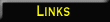
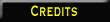
|
This document describes the simple process required to adjust
the Pugh-O-Spark magneto on the Wildebeeste line. This advice
is appropriate for machines manufactured in Scunthorpe and those
assembled in Argentina, although there are a couple of minor
differences in the latter that will be mentioned in the text.
Note that the Empire Wildebeeste Tropical (instantly recognisable
by the bamboo primary chain-case) uses a modified Pugh-O-Spark
to combat the engineer's fears of typhoons and tropical floods
and so, before embarking on this maintenance procedure, you first
need to melt off the 3lb of tar sealant.
Schedule
Magneto clearances should be checked at the regular 500 mile
major service intervals.
Description
As is so typical of Hurley-Pugh, the design of the Pugh-O-Spark
ignition system is a sight to behold. Young Alaric was unhappy
about the usual system of connecting the magneto directly to
the crank and then having some form of contact breaker arrangement
to allow for timed sparks. The constant drag of the magneto introduces
frictional losses, and the contact breakers available at the
time had only limited life-spans. Therefore, the Pugh-O-Spark
uses a different approach. The rearward facing side of the conrod's
big end is toothed. As the conrod rotates around the crankshaft,
every revolution its teeth mesh with the teeth on the gearwheel
at the end of the magneto. Thus, the action of the crankshaft
and conrod themselves provide a regular "kick" to the
magneto; each "kick" generates power for the spark.
The astute among you will realise that, as such an arrangement
will provide a spark on every revolution of the crank, the Hurley-Pughs
operate a "wasted spark" ignition system as, on every
other revolution, the spark will occur while the exhaust port
is open. This is not a problem, though, as due to the side-valve
design of the engine it is common for uncombusted charge to be
present in the inlet chamber that the additional spark ignites.
This doesn't increase power output as there is no compression
at that moment, but the extra flame does help to clear the exhaust
of carbon. Truly, this is the work of genius.
One implication of the Hurley-Pugh magneto arrangement is
that it is crucial that the magneto gear's teeth are in exactly
the right position to mesh with the teeth on the conrod when
it comes past. If this is not the case, splintering of the gear
teeth will occur, the debris will fall into the crankcases and
quickly cause the oil pump to seize - Hurley-Pugh did not fit
an oil strainer in the sump as the total loss lubrication system
means that the oil pump normally only sucks in fresh oil. To
ensure the correct alignment of gear teeth, there is first a
friction brake - in the form of a leather washer - on the magneto
shaft to prevent excessive rotation of the gearwheel, and second
the magneto itself is shimmed to locate it in precisely the correct
position. Incidentally, it is also by use of these shims that
adjustment of the ignition timing is performed.
Gaining Access
First remove any leg guards, fairing panels, engine bars and/or
auxiliary fuel and oil tanks that may be blocking access to the
engine. Such additions depend on the model. In the case of the
Gentleman's Twin-Outrigger Combination, remove both sidecars.
Remove the cylinder head and cylinder. Finally, remove the seat
(remembering to "safe" the ejection charges if fitted),
fuel tank, main oil tank, carburettor, spark plug, battery and
starter motor.
Removal
Now that access has been gained, put a 3 3/14" socket
on the exposed end of the crankshaft and rotate the crankshaft
in a clockwise direction until the engine is at 12 degrees before
Top Dead Centre. There aren't any alignment marks on the crankshaft
to mark this position, so you'll need a timing disc to locate
this point. The Hurley-Pugh Enthusiasts Club can supply one that
will fit on the recessed crankshaft for 73 pounds sterling.
With the crankshaft in the correct position, remove the six
bolts that secure the magneto to the top side of the crankcases.
You will notice that all of the bolts are different lengths -
it is crucial that these are replaced in the correct holes otherwise
you will lock the gearbox solid. Underneath the magneto you will
almost certainly find one or more thin shims, fitted by previous
owners. Hurley-Pugh itself did not actually shim the magnetos
when the engines were originally manufactured. Instead, Bill
"Masher" Stubbings precisely adjusted the magneto's
mounting points by the careful application of a large hammer.
If you look closely, you'll probably still be able to see the
dents in the top of the crankcase where "Masher" skilfully
wielded his scarred hammer. As Hurley-Pugh did not shim the magneto
it didn't produce any shims; again, the Hurley-Pugh Enthusiasts
Club can oblige with a set of paper shims for a reasonable 280
pounds complete.
Inspection
With the magneto removed, examine the teeth on both the gearwheel
and the conrod for signs of distress. Any evidence of chipping,
bending, burring or missing teeth will require replacement of
both the magneto gear and the conrod, as well as a complete engine
strip to remove the debris.
The leather friction washer can be found between the gearwheel
and the magneto. To inspect this, use a blowtorch to heat the
gearwheel to cherry red and use a 400lb press to ease it off
the shaft. The heating process usually destroys the leather washer
so it will need to be replaced regardless. Note that the washer
is made from treated rabbit skin; some unscrupulous suppliers
are selling washers made from inferior cow leather but these
parts will not impart the correct amount of friction so should
be avoided. The easiest way to test if a washer is from cow or
rabbit leather is to send it off for DNA testing.
Adjustment of Friction Washer
The precise amount of friction that the washer imparts on
the magneto shaft is crucial to ensuring correct alignment of
the gear teeth in operation. Adjustment is obtained by moving
the gearwheel slightly in or out on the shaft. The friction is
at the correct setting if, with the magneto at operating temperature
(60 degrees centigrade for European models, 70 degrees for Empire
models - pad the magneto in clean towels and put it in the family
tumble dryer until it is at the correct temperature) you should
be able to ease the ungummed edge of a Rizla Green King Size
cigarette paper - note, NOT Rizla Red - between the magneto body
and the washer. If there is insufficient clearance, allow the
magneto to cool then prise the gearwheel away from the magneto
with a large tyre iron. If there is excessive clearance, tap
the gear with a hammer.
Adjustment of Shims
With the friction washer correctly adjusted, if you are re-using
the original gearwheel and conrod, replace the magneto - with
any original shims - and torque the bolts down to 60ft-lbs for
those on the rear and 65ft-lbs for those at the front. If you
have replaced the gear and conrod, use 12 paper shims as a starting
point and, again, torque down the magneto bolts. As Hurley-Pugh
used as many mounting points as possible to support the weight
of the sizeable fuel and oil tanks, including the magneto, replace
the battery, carburettor, oil tank and fuel tank. Fill the fuel
tank half-full with four star and the oil tank with the normal
grade of lubricant. It is vitally important that the fuel tank
is replaced for this stage as the weight of it alters the clearances
for the magneto. Now, bend a 3 thou feeler gauge (4 thou for
the Argentinean models, as Johnny Foreigner wasn't as good at
manufacturing tolerances) into a Z-shape to allow it to be inserted
into the mouth of the crankcases and check the clearance between
the teeth of the conrod and magneto gearwheel. If a slight drag
is felt then all is well and the machine can be put back together.
If not, remove the fuel and oil tanks, battery and carburettor,
unbolt the magneto and re-shim. Repeat this process until the
clearances are correct. Note, it is advised that a new feeler
gauge is used each time as they tend to bend slightly too easily
and so can give incorrect results.
Testing
With the motorcycle now in one piece, follow the usual starting
procedure but with the main ignition off. Use a wooden wedge
to prop the automatic exhaust valve lifter open, release the
auxiliary starter clutch and listen carefully for any quiet knocking
or grinding sounds from the magneto. Of course, the noise of
the unsilenced two-stroke starter motor may make such low-level
sounds difficult to ascertain; with experience, though, one can
readily notice the sound of a maladjusted Pugh-O-Spark.
Once you just hear the normal sounds of a healthy Hurley-Pugh,
the process is done. Happy motorcycling! |